Lean Six Sigma Consulting in Massachusetts
Contact Us
The Six Sigma Lean Process
When a company develops a product or service, Lean Six Sigma Experts of Massachusetts is the company to contact to remove anomalies, service flaws, or defects. In general, Lean Six Sigma employs a control map of elements that correlate to the material development process. The accepted products and procedures must fall into a certain category when translated into the points on the table. Furthermore, points that are outside of the given limits are referred to as system faults.
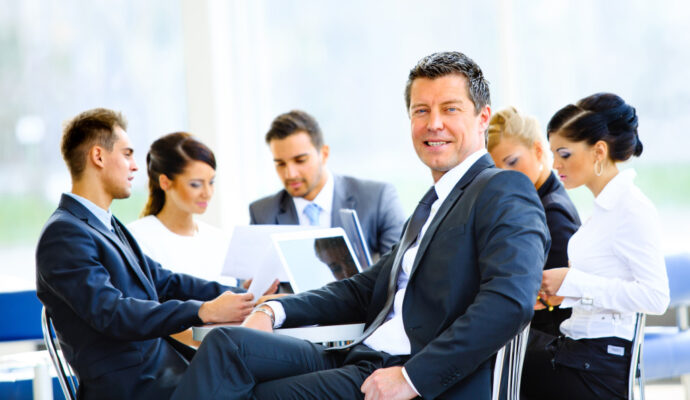
The Benefits of Using Lean Six Sigma of Massachusetts
- Assist you in developing your corporate strategy: Lean Six Sigma is vital to the success of a company. When a company decides on its job, priorities, and conducts a SWOT review, using Six Sigma methods helps you to concentrate more effectively and reliably on areas for improvement. For a company implementing Lean Six Sigma to become an industry leader, it will increase performance, strengthen internal operations, keep the lowest-cost vendors, and avoid unneeded issues.
- Maintains employer and employee motivation: Entrepreneurs and company owners always neglect that productivity is based on employers and workers. This translates to greater productivity, which leads to increased service revenue. Employees, on the other hand, must be inspired and empowered to work and excel regularly. Companies that retain their staff actively see a 25% to 50% increase in productivity. Implementing Six Sigma problem-solving approaches and tools successfully facilitates job advancement and helps to create a balanced corporate culture of knowledge sharing and employee participation.
- Assist you in drastically reducing turnaround times: Companies often meet deadlines. This is mostly attributed to increased project scope and recent management policy shifts. Using Lean Six Sigma techniques, you can form expert teams within the company. Professionals with a wide range of professional skills are often in demand. This unit investigates the factors that can jeopardize the project’s long-term progress. The team will then be pushed to come up with ways to minimize the possible repercussions. Several prestigious Six Sigma companies have reported a 35% cut in cycle times.
Increasing expertise is necessary to create frequently asked questions. Evaluating prospective partners and choosing the best Lean Six Sigma partner is the next thing that is required for program development, and the choice of any additional partner, contractor, or supplier is vital. Any of the following questions will give you an idea of the types of answers you can expect:
A company like Lean Six Sigma Experts of Massachusetts will collaborate and form a cross-functional implementation team with you and other key stakeholders in the company. You should choose a partner who is well-versed in coaching, strategies, and best practices. Participants may have practical experience using some of the existing process management approaches to obtain market goals, as well as knowledge of the overall company strategy and customer approach. If you only have implementation instructions during the first stage of the startup process, this may be a red flag. Any Lean Six Sigma implementation at an enterprise level should begin with an understanding of the customer strategy and current changing management and process transformation cultures, supplemented by a plan that adapts the solution to those realities. Project evaluation is critical when implementing Lean Six Sigma into a company's ecosystem. The separation of the conceptual focus areas into project ideas is one of the most critical aspects of this process. The project procurement process will help to ensure that high-value, well-established projects are found and linked to strategic targets, reducing project lead times and internal corporate capital shortages. Following the identification of plans, a consultation should be held with key stakeholders to validate timely findings and prioritize initiatives. There are several Lean Six Sigma systems to be identified, as well as other activities to be discussed. The startup process can be seen as a project charter for selected Lean Six Sigma project proposals, which should provide the company case for each project. At this point, we're also defining benchmark standards, which will enable us to track process performance and improvements. It is important to apply the technique systematically over time; the team must be aware of its tasks and responsibilities. To accomplish the team's objectives, each participant must be critically measured. Similarly, in the workplace, Lean Six Sigma should be seen as a long-term company rather than a sequence of steps; all must be changed. The approach taken by management to the plan paves the way for the future; tradition and method are more critical than a company. Long-term commitment is required; the strategy must be expressed in policy and the institutional environment. To evaluate outcomes, the company must present and apply data and estimates, and consider compliant conduct in organizational culture. It is important to consider and reward recent achievements. "We are a customer-driven company!" some people tell us. That's fine, but what separates traditional firms from customer-centric companies? Customer-driven companies, on the other hand, are dedicated to delivering high-quality products and services that meet the needs of their customers. The Lean Six Sigma Experts of Massachusetts have tools as well as a system for defining and measuring customer requirements. "What Success Looks Like" is now clear. Do you remember the sentence "poor systems cause 95% of errors"? Errors are known as "a person's matter" or "a human fault" in some organizations. They try to patch people's processes using broken systems. The emphasis of a Lean Six Sigma methodology is on industrial efficiency and Lean systems. Efforts are being made to upgrade systems to reduce errors. Human presence in routine work should be reduced or removed. This removes the monotony of repetitive tasks and allows employees to concentrate on higher-value events. Individuals can practice several techniques from a variety of sources daily. Since they are implementing the techniques and implementing them within their organizations, they can teach colleagues about them; all of this leads to professional development. What is your new customer onboarding process?
What are the project's collection and configuration procedures?
Is Lean Six Sigma a series of change initiatives?
What advantage does the consumer gain?
What advantage do employees gain?
There are so many areas or regions where we offer these services with most of them being cities.
However, if you need any of these services, you need to contact us. The list below comprises the areas where we offer these services.