What is Lean Six Sigma in Massachusetts?
Contact Us
If you want to learn more about Lean Six Sigma?
When Motorola launched the Six Sigma initiative in 1987, it signaled the beginning of a new way of thinking. The demonstrated quality control methodology has had a fascinating growth history over time. It began slowly but quickly gained attention as a result of its exceptional outcomes. As Jack Welch, then-CEO of GE and now-CEO of AlliedSignal launched Six Sigma in the 1990s, it was noted as having significant early growth potential. Many companies have since embraced and reaped the advantages of this strategy.
Six Sigma was once seen as a “management fad” by the general population rather than a “quality control system.” Six Sigma is a methodology that has helped Fortune 500 companies reap billions of dollars in return on investment. Today, however, it is generally accepted that it is no longer just a management fad.
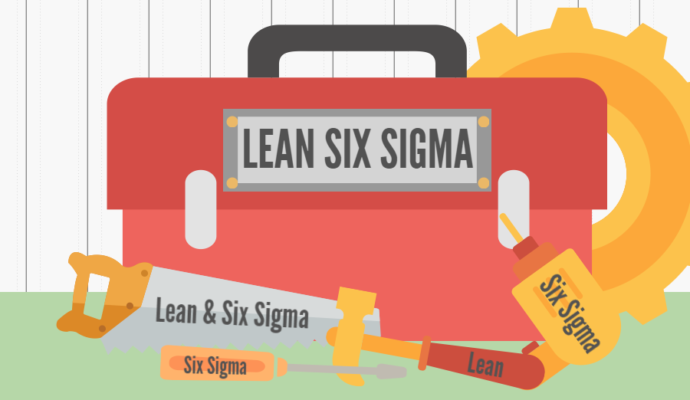
The Advantages of Using Lean Six Sigma
Six Sigma leads to substantial time and expense savings, as well as greater accuracy of processes. When used with caution and conscientiousness, the Six Sigma approach is often reliable. It maintains and fosters a sense of customer well-being; any good company needs to retain its current clients. Customers can opt to stick with you rather than check out another service or go to a competitor’s brand. Can you count the number of customers who are unhappy with the services you provide? Many companies would be unaware of this fact and will create strategic growth strategies without considering customer loyalty.
The use of the Six Sigma process has reduced the challenge. Conduct a dipstick survey to assess the characteristics of your service or product that are needed to successfully engage consumers. When planning your business expansion strategies, make sure you don’t forget something that might entice your clients.
A strategy is needed when incorporating business insight, performance, emerging technology, and rigorous quality management in today’s industry. If you want the company to be recognized as an industry pioneer? Will you aspire to achieve a major competitive edge in the industry’s marketplace? Six Sigma methodologies can be used to optimize the productivity of available capital assets.
FAQs
The future seems to be bright and the rate of change quickens with each passing year. The primary role of management in an organization is to design and implement systems. Most processes and value creation systems for customers and companies are never-ending. You might come up with new ways to draw buyers to retain them. Customers are receiving goods and services in novel ways as a result of logistics and new technologies. Customer preferences can shift rapidly. Today's amusing suggestion becomes a must the next day. Organizations must transform and evolve or die, so rising to the task of reform is more critical than ever. Lean and Six Sigma are excited about the shift. This technique encourages both accuracy and timeliness. Both product and service strategies require creativity. The shift in operations is a way of life, not a process. Managers should use the "Lean Six Sigma" methodology (a compilation of management strategies and best practices) as a starting point for making improvements. Both operators and engineers are recruited by Black Belt, and most applicants for operator and engineer positions are checked for Black Belt capability. This means that Six Sigma is aligned with the company's objectives. Given the importance of selecting the right Lean Six Sigma partner, it just makes sense to answer the most frequently asked questions by the people interested. The below are some of the most commonly asked questions, along with some of the more possible answers: At the very least, your Lean Sigma affiliate should have an accomplished Six Sigma consultant who can have guidance and instruction for your Master Black Belt. A Master Black Belt specialist should have real-world expertise and be at home in the company's atmosphere and with its employees. During the planning process, candidates can develop strategies and apply them to real-world programs. Course assignments can enable trainees to be connected to project results and to apply their skills. Keeping the projects on target necessitates dollar realizations and timeline lag. Participants and system issues should be identified by the Master Black Belt. To make real progress, it is important to evaluate the company's readiness to adopt Lean Six Sigma. Your implementation partner will detail preparatory steps that will lay the groundwork for the ongoing deployment. This includes analyzing recent trends and services in progress, as well as defining plans for future initiatives. A void report should include a customer and company awareness analysis, as well as a review of defined goals. This function aids in the discovery of potential implementation problems that can be resolved. Mathematical approaches were used to validate the Six Sigma measurements and performance. Six Sigma calculations are based on inferential statistics and probability hypotheses. Six Sigma, on the other hand, is more than just numbers. It is a methodology that consists of several tools for defining customer services and measuring service quality. Six Sigma has the benefit of reducing the number of uncertainties, providing administrators with a better picture of what a successful system looks like, and helping them to judge performance more accurately, in the eyes of consumers. To be a Six Sigma specialist, you must have a strong dedication to providing excellent customer service, the courage to do a baseline review regularly, and the capacity to articulate statistics. The Lean approach is a low-cost way of meeting project goals (called Muda in Japanese). Taiichi Ohno defines seven levels of waste in systems (TPS fame). To best serve customers, it is important to increase service and identify and avoid duplication. Lean and Six Sigma methodologies are used to optimize processes and the overall performance of the company. Lean is all about improving processes, balancing systems, and increasing efficiency. Six Sigma is all about development, success, results, and efficiency. What is the significance of Six Sigma?
What Is the Process of Lean Six Sigma?
How do you handle project-based classes?
How can you integrate the software with the job that our company already does?
Is it necessary for me to study statistics because Six Sigma is based on statistics?
What's the distinction between Six Sigma and Lean?
There are so many areas or regions where we offer these services with most of them being cities.
However, if you need any of these services, you need to contact us. The list below comprises the areas where we offer these services.